Riveting Tungsten Boat
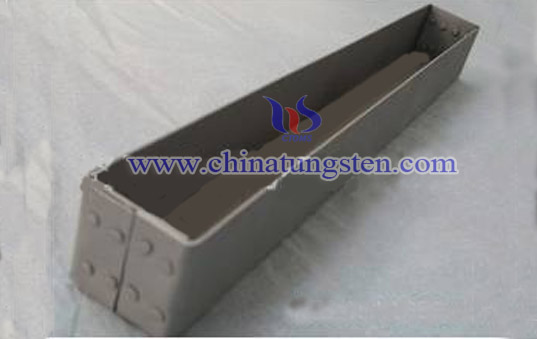
Introduction
Riveting two tungsten plates with rivet to form the shape of tungsten boat. The manufacturing processes are drilling holes → (burring) → inserting rivets → using backform up to the rivets → forming the final product with rivet bucker. A great strength is the main character of riveting wolfram boat, due to the rivet connection, the connection tightness of its joint is better. Riveting W-boat can be formed to a large size.
Manufacturing Process
Riveting can be divided into active riveting, fixed riveting, sealing riveting. Active riveting conjunction can be rotated with each other, whose flexibility is strong. Conjunction of fixed riveting cannot active. Sealing riveting is to use lockbolts, threaded hollow rivets, self-plugging rivets in some parts which require no oil leaking, water leaking and gas leaking. Firstly drilling holes in the connection part of tungsten plate, and then burring. Next is to insert the wolfram rivets, and finally against the rivet with backform, using rivet bucker to form wolfram boat.
Advantages
The riveting and bolting joint of riveting W-boat belong detachable connection, so it is possible to change the vulnerable parts which has a good sealing performance. Tungsten boat made by sealing riveting can greatly eliminate the gap of its structure, blocking pathways of leaking. It is easy for riveting W-boat to check and rectify the fault. Tool using is flexible, simple and inexpensive.
Disadvantages
Geometry of rivet and BHF and clearance of concave die have a greater impact on the quality of riveting.
Physical Properties
Color | Melting point ℃ | Density g/cm3 | Purity % | Allowable Error(mm) |
silvery white | 3407 | 19.35 | 99.95 | ±0.1 |