Tungsten Rod Application - Spot Welding
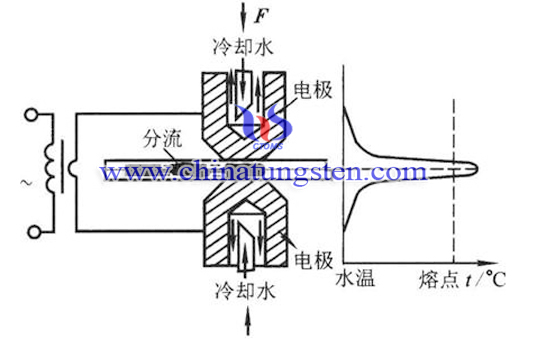
Tungsten Rod Application - Spot Welding
Tungsten rod application refers to a pure tungsten rod designed for spot welding process. When welding, clean weldmemt surface at first, then install the plank stuff, put it between two cylindrical copper electrodes, pressing it. Spot welding is is a process in which contacting metal surfaces are joined by the heat obtained from resistance to electric current. It is typically used when welding particular types of sheet metal, welded wire mesh or wire mesh. The basic spot welder consists of a power supply, an energy storage unit (e.g., a capacitor bank), a switch, a welding transformer, and the welding electrodes. The voltage needed for welding depends on the resistance of the material to be welded, the sheet thickness and desired size of the nugget. During the welding process, tungsten rod is better not to touch the pieces, if not, the distance should also be controlled within 3mm, and 1mm is the best.
Tungsten Rod and Copper Rod
Traditional spot welding electrodes use copper rods. Although copper rod has high purity with fine organization, and its oxygen content is very low, and other excellent performance, in the spot welding, temperature of the welding point of copper rod electrode is low, thus resulting in rosin joint, affecting the quality of the welds. Because tungsten rod has high temperature strength and creep resistance and thermal conductivity, electrical conductivity and electron emission properties, it can increase the temperature spot welding point to avoid rosin joint phenomenon, thereby improving welding quality and reduce the rate of defective welding. Defective rate is decreased from 0.6% to 0.2%.